Cover Story: Grassoline in Your Tank: Myths and Realities about Biofuels
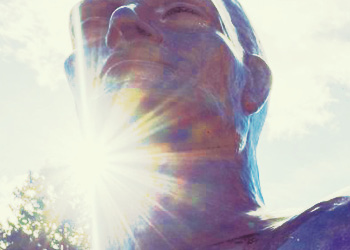
In the world after oil, cellulosic ethanol is among the more promising biofuel alternatives—despite some prevalent myths to the contrary.
The age of oil is ending. Even if we could afford to borrow over $1 billion per day indefinitely to import oil, we just can’t afford the cost of our oil addiction in terms of national security dangers, environmental damage and economic losses. Biofuels are among a small handful of petroleum alternatives that can simultaneously provide enhanced national security, environmental improvements and opportunities for broad based economic growth.
Unfortunately, many myths and misconceptions exist about biofuels. I will deal with some of the myths about ethanol, by far the dominant current biofuel. These myths include: 1) the “people are going to go hungry because of ethanol” myth, 2) the “there isn’t enough land to produce enough ethanol anyway” myth, 3) the “it takes more energy to make ethanol than you get from the ethanol” myth and 4) the “ethanol will always be more costly than gasoline” myth.
BACKGROUND ON ETHANOL PRODUCTION
All fuel (and sippin’) ethanol is the same. It is made by fermentation of sugars. The sugars can come from sugar cane (Brazil), or from corn grain (U. S.). “Second generation” ethanol, called cellulosic ethanol, will be produced from the sugars in plant cell walls. Cellulosic ethanol can be made from virtually anything that is or ever was a plant including: wood chips, urban waste, straw, crop wastes, hay and yard trimmings, and on and on. We can even grow “energy crops”: trees (willow and poplar are promising species) and highly productive grasses such as switch grass and Miscanthus for their energy content and then convert them to ethanol.
Maybe a more picturesque and accurate name for cellulosic ethanol is “grassoline.” Got the image in your mind? Your lawn clippings turned into fuel for your car? Yes, that’s right.
Now let’s deal with the four myths above.
MYTH #1: PEOPLE ARE GOING TO GO HUNGRY
The idea of turning corn into ethanol conjures up visions of our cars taking grain out of the mouths of hungry people. Actually, well over 70 percent of the grain we grow is used to feed animals, not people. We really don’t “grow food” in this country, or in most of the developed world. We grow animal feed instead and then we eat the meat, milk, eggs, cheese, etc. that the animals produce. We have about 800 million acres of cropland and animal pasture in this country. It is easy to show that about 500 million of those acres produce animal feed, not food consumed directly by human beings. If you want to increase grain supplies (and decrease grain prices, thereby putting a lot of poor Third World farmers out of business), then become a strict vegetarian.
While no one wishes to minimize the problem of hunger in the world, this issue of “food vs. fuel” requires facts and logic, not emotionalism. There is about 5 cents worth of corn in that $3 box of corn flakes you just bought at the store. Increased corn prices affect the cost of a few things at the store, but the cost of fuel to move all those groceries around affects the price of literally everything. Keeping a lid on gas prices by converting some of our surplus grain into ethanol will help hold down food prices. Actually, the use of corn to make ethanol is self limiting. As demand for corn increases, its price will rise to the point where it will no longer be economical to produce ethanol from corn.
Increased ethanol production and the accompanying increase in corn prices from about $2.20 per bushel a few years ago to around $3.50 or so per bushel today is a very good thing. First, many of our rural communities near ethanol plants are enjoying a prosperity they have not seen in a long time. Second, many poor farmers around the world are now able to get more money for their products, and thus can provide better for their families. Cheap, tax-subsidized U. S. grain has long been a key factor undermining agricultural societies around the world. The U. S. taxpayer has also benefited. Most of the tax subsidies paid to corn farmers have disappeared with rising corn prices, saving the U. S. Treasury over $7 billion a year.
Finally, as “grassoline” (cellulosic ethanol) technology develops we will almost certainly produce enhanced animal feeds as co-products with ethanol from this technology. This will further reduce “food vs. fuel” conflicts by reducing the amount of land required to both feed and fuel us. In essence, the land will do double duty by producing both animal feed and fuel. Now, more about the land issue.
MYTH #2: THERE ISN'T ENOUGH LAND TO MAKE LOTS OF ENTHANOL
We can probably make about 15 billion gallons per year of ethanol from corn, which is about 10 percent of our annual gasoline consumption, before we reach its limits. The Brazilians can probably make a similar amount from sugar cane. While that doesn’t fundamentally change our dependence on imported oil, it is still a lot of fuel that we are not paying other nations, many of them hostile, to produce for us. Jim Woolsey, former director of the CIA, has pointed out that the twin pillars of international terrorism are the illegal drug trade, and the oil trade. Woolsey also correctly states that the war on terror is the only war in which we have paid for both sides—by our taxes on our side and by our oil imports on their side.
Nonetheless, it is simply true that there is not enough corn or sugar in the world to replace more than a small fraction of our total oil needs. But the situation is much different for grassoline. The U. S. Dept. of Agriculture and the U. S. Dept. of Energy recently issued a report indicating that our country can sustainably produce about 1.3 billion tons of cellulosic materials (wood, grass, straw, etc.) per year, enough to make well over 100 billion gallons of ethanol. The energy content of this much cellulosic material is about equal to the energy content of 3.5 billion barrels of oil—which happens to be the maximum amount of oil the U. S. ever produced before our domestic oil production peaked and began declining in the early 1970s.
Other highly qualified sources are even more positive about the potential of grassoline. Ceres, a leading plant biotechnology company, believes that average yields of energy grasses such as switch grass can increase threefold to about 15 tons per acre per year in a relatively short time. The giant grass Miscanthus sinenis is probably even more productive, with yields reported already of over 20 tons per acre per year. Given that corn yields have increased by over fivefold in the past 30 years or so, the increased grass yields envisioned by Ceres and others would seem to be well within reach. If, out of 800 million acres of crop and pasture land, we devote 100 million acres of land to grow grasses yielding 15 tons per acre we can produce about 150 billion gallons of ethanol per year…roughly the same volume as our total gasoline consumption. Animal feeds will probably be co-produced with grassoline, further reducing the amount of land required. Reasonable scenarios have been proposed that envision no new land devoted to agriculture and that still replace all oil imports with domestically produced grassoline. Grassoline therefore has the potential to be a very, very large business and land availability is simply not a limit to the growth of the industry.
MYTH #3: IT TAKES MORE ENERGY TO MAKE ETHANOL THAN YOU GET OUT OF IT.
In some ways, this is the most irrelevant of all the myths surrounding ethanol. The “net energy” idea has been promoted by David Pimentel of Cornell University and his coworkers for over 25 years. He criticizes corn ethanol (and more recently cellulosic ethanol) as requiring more fossil energy to produce them than these biofuels release when burned. Dr. Pimentel defines “net energy” as the fuel’s heating value minus the sum of all the fossil energy (coal, natural gas and petroleum) inputs required to produce the fuel.
Net energy is an irrelevant, almost silly, concept because it lumps all forms of fossil energy together as if they were identical. Net energy treats a megajoule (MJ—a measure of energy content) of coal as equivalent to a MJ of petroleum or natural gas. This is obviously wrong; otherwise we would not pay over five times as much for a MJ of petroleum as we do for a MJ of coal. The silliness of the net energy idea is shown by a simple illustration. Grind up some coal and put it your gas tank—then try driving. There is energy in the coal, but that energy is essentially useless to power your car. Still think that all forms of energy are equally valuable? They are not; and thus “net energy” is fundamentally in error.
This error is compounded by Pimentel’s failure to compare ethanol’s net energy with the net energy of gasoline. The comparison is easily done. Science, one of the most prestigious of scientific journals, last year published a graph comparing the amount of fossil energy (and other inputs) required to make 1 MJ of gasoline and 1 MJ of ethanol (from corn or cellulosics). From their graph, ethanol’s net energy is its energy value minus the sum of all the fossil energy inputs required to make ethanol. Based on 1 MJ of ethanol produced, net energy is calculated as 1.0 – (0.04 + 0.28 + 0.41) equals +27%. By comparison, gasoline’s net energy is 1.0 – (1.1 + 0.03 + 0.05) equals -18%. Gasoline’s “net energy” is worse than ethanol’s. Net energy is an irrelevant concept, but the comparison between ethanol and gasoline is very valuable. We could have been saved much confusion and trouble if Pimentel had ever compared ethanol’s net energy with the net energy of gasoline. Comparisons between our realistic alternatives are absolutely essential for good decision making.
The data of Figure 2 allow us to make another very important comparison: the amount of oil used to make gasoline versus the amount of oil required to make ethanol. Generating 1 MJ of gasoline requires 1.1 MJ of petroleum while only 0.04 MJ of petroleum is required to generate 1 MJ of ethanol from corn (Ethanol Today scenario in Figure 2). The reduction in petroleum required per unit of fuel energy delivered to the customer is therefore (0.04-1.1)/1.0 equals 106%. For corn ethanol, this is like improving vehicle mileage per unit of petroleum consumed by (1.1-0.04)/0.04 equals 26.5 or nearly 27 fold, effectively a 2700% increase in vehicle miles traveled per gallon. So if your new car gets 30 miles per gallon, on ethanol you are effectively getting (30 x 27) or 810 miles per gallon of oil used. Not bad mileage! We have no other alternative liquid fuel that so greatly increases miles per barrel of oil.
MYTH #4: ETHANOL WILL ALWAYS COST MORE THAN GAS
When corn is about $3.20 per bushel, ethanol can be produced from it at the energy equivalent cost of gasoline when oil is $65 per barrel (a gallon of ethanol has about 70 percent of the energy content of a gallon of gasoline). The cost of ethanol made from corn is likely to decrease somewhat over the next five years or so as production costs decrease and corn prices stabilize. The Brazilians have successfully reduced the cost of ethanol made from sugar cane by a factor of three over the past couple of decades. On an energy equivalent basis, ethanol from sugar cane is now cheaper than gasoline. Do you want to take any bets on where gas prices are going to go from here? Hint: we aren’t finding oil as fast as we are burning it.
For grassoline, the prospects are even better. For commodity products, only two costs matter in the final selling price: 1) the raw material cost and 2) the cost of processing required to convert the raw material to products. Cellulosic raw materials are so cheap that very low cost ethanol can be made from them as the conversion technology matures and processing costs decrease. Careful economic analyses, including analyses done at MSU, indicate that grassoline can eventually be produced for about $0.60 per gallon, or less than $1 per gallon of gasoline (energy equivalent basis) using mature technology. Now that is something to give the oil dictators a bad night’s sleep!
Two things must be done to drive down processing costs. First, we need to build some large scale plants and “learn by doing”. There are many cost reductions that can only occur in large scale commercial practice. Last February the U. S. Department of Energy announced that it will partially support six large scale cellulosic ethanol plants using different raw materials and different processing technology combinations. In July, Mascoma Corporation, a leading cellulosic ethanol firm, announced that it will build its flagship plant here in Michigan, without any Federal support at all. Mascoma is bankrolled by several highly successful venture capital firms—yet another sign that grassoline is increasingly regarded as a viable emerging industry.
Second, laboratory research aimed at the most cost sensitive areas of the system can also reduce ethanol production costs. Hundreds of millions will be spent in this area over the coming years. Michigan got another leg up in this emerging industry in June when MSU and the University of Wisconsin won a five year, $125 million dollar research project to develop improved cellulosic ethanol technologies and other advanced biofuels. MSU has some of its own advanced technologies in this research mix. Thus our state is in a great position to pioneer biofuels as we pioneered the auto industry.
We can’t afford our oil addiction any longer. Cellulosic ethanol is an attractive, potentially low cost alternative to petroleum fuels. Myths about ethanol are just that: myths. Grassoline will be in your tank sooner than you may think.
author’s note: Bruce Daleis professor of chemical engineering and former chair of MSU’s Dept. of Chemical Engineering and Materials Science. He is also associate director of MSU’s Office of Biobased Technologies. He graduated from the University of Arizona in 1974 and received his doctorate from Purdue University in 1979. In 1996 he won the Charles D. Scott Award for contributions to the use of biotechnology to produce fuels, chemical and other industrial products from renewable plant resources.
MSU RESEARCH EFFORTS ON THE BIOECONOMY
A number of research projects related to the bioeconomy are currently ongoing at Michigan State. Here are some of the major ones:
- Bioenergy Research: MSU is partnering with the University of Wisconsin-Madison in the Great Lakes Bioenergy Research Center (GLBRC), one of three centers established by the U.S. Department of Energy (DOE). MSU's $50 million portion is the largest federal grant exclusively for research endeavors in university history. The research focuses on breeding new varieties of bioenergy plants, developing new processing techniques and agents to break down cellulose, improving the microbial and chemical processes that convert biomass to energy, enhancing biofuel sustainability, and integrating new technologies, including genomics and computational methods, into bioenergy research.
- Getting Biofuels into Gas Tanks: Petroleum fuels are blended to offer maximum power and efficiency in engines designed to take advantage of the fuel's properties, whereas biofuels have not been designed for existing engines and thus often perform less than optimally in current engines. Using a $4.7 million DOE grant, a team of MSU scientists is working to change that. Chemical engineers Dennis Miller, Kris Berglund, Ramani Narayan and Carl Lira and mechanical engineers Harold Schock, Farhad Jaberi and Tonghun Lee are working with the Ford Motor Co. to create new fuels from renewable resources that are more complex and sophisticated than existing biofuels, as well as engines that can take full advantage of these next generation biofuels. This is one of the first times that research on biofuels and engines are integrated in the same project.
- Growing the Bioeconomy Below Zero: MSU researchers are working closely with Swedish scientists and entrepreneurs to create new bioproducts and bioprocesses. Kris Berglund, University Distinguished Professor of forestry and chemical engineering and materials science; Steve Pueppke, director of the Office of Biobased Technologies; and Ray Miller, research forester and Upper Peninsula forest properties manager, took part in a trip to Sweden with Gov. Granholm and representatives of the Michigan Economic Development Corp. and Michigan Tech University in August to foster business and research partnerships. Berglund has been instrumental in laying the groundwork for several Michigan-Sweden collaborations. In addition to his MSU appointment, he is also a professor in the Dept. of Biochemical and Chemical Process Engineering, at the Luleå University of Technology in Sweden. Berglund's collaborations have spawned enterprises in Michigan, Sweden and France and raised tantalizing possibilities for diversified biorefineries that crank out bioproducts ranging from fuels to chemicals. Michigan State and Michigan Tech have signed a cooperative agreement to create new collaborative research, outreach and economic development programs centered on fuels and energy made from forest biomass. The programs are overseen by an eight-member Renewable Fuels Working Group made up of four scientists from each university.
- Boosting Plant Oil Production: Plant oils are the most energy-rich biomass available from plants, and it requires very little energy to extract and convert them to fuels. Plant oils aren't widely used as a replacement for petroleum because of low oil yield per acre of crop. Christoph Benning, professor of biochemistry and molecular biology, and John Ohlrogge, University Distinguished Professor of plant biology, have made advances in reprogramming both oilseed crops and other crops to accumulate large amounts of oil at the right growth stage so the most oil per acre can be harvested.
- Turning a Cornstalk into a Fermentation Vat: Breaking down cellulose into simple sugars for fermentation into ethanol is a challenge for biofuel producers. Enzymes can do the work but make the process and the final product more costly. Researchers Bruce Dale, professor of chemical engineering and materials science, and Mariam Sticklen, professor of crop and soil sciences, have found a way to make a corn plant do some of the work by genetically engineering corn varieties to produce the necessary enzymes so the corn plant produces fermentable glucose. MSU has filed for patents on the first and second generations of this Spartan Corn, and licensing negotiations for the technology are underway.
- The Greening of Brownfields: Kurt Thelen, associate professor of crop and soil sciences, is growing soybeans, corn, canola and switchgrass on two acres in southeastern Michigan. Nothing unusual about that—except that the crops are on an EPA Superfund site, also known as a brownfield. Thelen's research is exploring two intriguing possibilities. Can the brownfield produce crops that have the quality and yield for biodiesel or ethanol production? And can the biofuel crops help clean up the contaminated soil? The research project is a partnership between MSU, Chrylser LLC and NextEnergy.
- Pretreatments for Biomass for More Efficient Ethanol Production: MSU has a patented process called ammonia fiber expansion (AFEX), developed by Bruce Dale, professor of chemical engineering and materials science, to pretreat biomass with concentrated ammonia. AFEX makes the breakdown of cellulose more efficient. Using enzymes alone, about 15 percent of cellulose is broken down into simple sugars; when AFEX is used before adding enzymes, more than 90 percent of the cellulose is broken down.
- For more information, visit www.bioeconomy.msu.edu.
--Compiled by Jamie DePolo, ’84, M.A. ’93, communications manager for the Office of Biobased Technologies and the Michigan Agricultural Experiment Station.