Feature: Major Gift for MSU Engineering Advances Computer-Aided Design
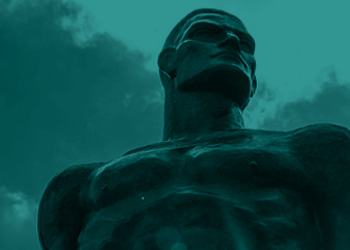
A major corporate gift provides MSU students with state-of-the-art computer hardware and software used in car design and engineering.
It can happen in the shower, at a stoplight, on the treadmill, in the check-out aisle. A great idea strikes—fast—hitting us cold out of who-knows-where. So it must be frustrating to experience one of these lucid moments of inspiration, only to wait another three or four years until it's finally put into play. Such has been the dilemma of auto makers in America, where it can take roughly 50 months before a great idea gets wheels. Thanks to a new alliance between four forward-thinking companies and Michigan State University's College of Engineering, however, we're now poised to up that pace.
PACE, the Partnership for the Advancement of CAD/CAM/CAE Education, is the unified effort of General Motors, Unigraphics Solutions (UGS), Sun Microsystems, and Electronic Data Systems (EDS) to more amply equip up-and-coming engineers. The four organizations are committing $190 million (fair market value) in computer hardware, software, training, and support to 40 key universities in the areas of computer-aided design (CAD), computer-aided manufacturing (CAM), and computer-aided engineering (CAE).
Michigan State University has been designated to receive the first and largest of the gifts-in-kind: 110 work stations, training, and support valued at $30 million. Other universities in the U. S. and Mexico will follow in the next three years. 'It used to be that designers would dream up the overall design of a product and then those involved in engineering analysis and in manufacturing would determine if the products were feasible or could be made,' explains Nicholas Altiero, chairperson of the Dept. of Materials Science and Mechanics and the partnership's principal liaison from MSU. 'PACE is hoping to stimulate universities to prepare 'designing engineers'—engineers who can function in teams that are capable of doing it all concurrently.'
Central to the program is the use of Unigraphics Solutions 3-D solid-modeling software, the industry standard in CAD/CAM/CAE technology, typically considered too pricey for most academic department budgets. Now, with the availability of this state-of-the-industry software, students at MSU are developing proficiency in computer skills that are of utmost relevance and marketability in today's automotive and manufacturing industries.
'We live in a world of solid models,' remarks Jay Wetzel, vice-president and general manager of General Motors Technical Centers, giving shape and substance to his argument that 3-D solid modeling is the future of automotive design. 'In the days when everything was 2-D, we spent all our time trying to figure out which line we were looking at,' he notes with a grin.
With PACE's gift, students can create a line drawing along the X, Y, and—what puts the 'three' in 3-D—Z axes, and, with one mouse click, visualize how that component would appear painted, shaded, and rotated at every possible angle as if it had actually been manufactured. The ability to view brackets and bolts rolling and tumbling across a computer screen—a virtual cosmos of car parts—is only the beginning, however.
Of greater importance is the opportunity for students to make use of 'parametric modeling' as they undergo the entire design process. With parametric modeling, students can tweak the dimensions, orientation, and shape of any given feature—a.k.a. the model's parameters—and immediately witness how those changes affect the overall design. If a student opts to up the size of an engine, say, the program can either alert her that there will be interference with the hood, which she'll need to fix later, or, if the two features are linked, the program will resize the hood accordingly.
Robert Chalou, academic specialist for the Department of Materials Science and Mechanics, instructs Engineering Graphic Communications, the Unigraphics-based freshman design course that is the starting point for many of the college's undergraduate degree programs. Chalou says parametric modeling not only saves time and reduces error, it makes concurrent engineering possible, the fast-growing trend in manufacturing where design teams are able to grapple with various elements of the same project across continents, 24 hours a day. 'In concurrent engineering, all aspects of the design team are working simultaneously on a problem,' explains Chalou. 'That includes manufacturing, marketing, product design, and engineering. And what makes concurrent engineering possible is the CAD database that is central to all these different disciplines. If someone in one unit is making an update on a part, the other units have to be able to see those changes as they are being made—and you can only do that with a very powerful CAD package.'
'It's realtime teaming,' inserts Altiero, 'and it's where the engineering profession is headed.'
Michigan State University was selected as the premiere university to participate in the program because it meets PACE's strict criteria, namely: a long-term relationship with General Motors as a primary educational partner; strong product development and manufacturing curricula; adequate infrastructure of facilities, maintenance systems, and personnel to support the donated hardware and software; dedication to providing distance learning to students at GM facilities around the globe; and willingness to integrate Unigraphics software into the engineering curricula.
Already, 15 of MSU's courses in mechanical engineering, manufacturing engineering, engineering mechanics, and engineering arts have been redesigned to incorporate the sophisticated software and instrumentation. In addition to pioneering the program, Michigan State will help other selected universities get up and running by configuring software and hardware for them as well as providing technical guidance to their faculty.
As many as 90 of MSU's 110 new work stations will be dedicated solely to student use, with the other 20 donated primarily to faculty members to conduct research in such areas as biomechanical engineering, manufacturing, and finite element analysis. Faculty involved in the college's Institute for Global Engineering Education are planning to use the work stations to form long-distance design teams with participating universities in Mexico.
MSU's mini-baja team, a group of students who design and build cars capable of surmounting mogul-style hills and traversing 80-foot-deep lakes, are looking forward to putting one of the new work stations to use. According to Jeremy Short, a senior engineering mechanics major and veteran member of MSU's mini-baja team, the parametric modeling feature would have come in handy for the team as it prepared for last year's competition. 'One of the rear suspension arms interfered with a belt guard that we'd added at the last moment,' he recalls with modest disappointment. 'We didn't realize they were going to touch—and when they came together, the arm snapped in half.'
'This year,' he adds resolutely, 'with Unigraphics, we're putting everything—I mean, every nut and bolt is going to be drawn before it's ever on the car.'
Students also are able to test their designs, calculating such properties as fatigue, vibration, or stress and strain, and making sure the drawing will work before they actually build the prototype. Short says the new work stations will help make future mini-baja cars more competitive because students will be able to concentrate on the big picture. 'Back in the old days, a lot of our cars were very heavy,' he says, remembering when students used to model components with cardboard, striving only to make the car work, and worrying less about styling and efficiency.'